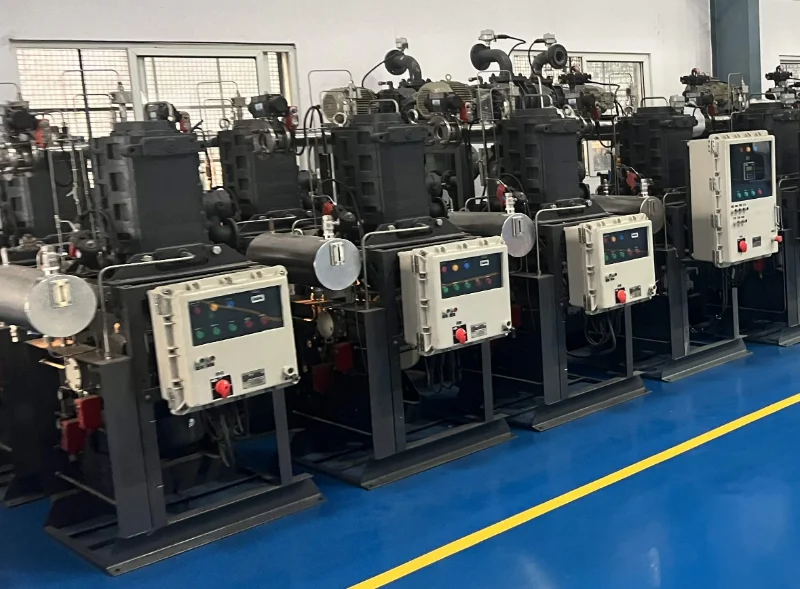
Vacuum pump efficiency is critical in industrial operations that rely on pressure control, air removal, or process precision. When configured correctly, a vacuum system can significantly improve output, reduce energy use, and minimise operational costs. Stanpumps plays a pivotal role in helping industries optimise vacuum performance through specialised engineering and a practical understanding of application-specific requirements.
System efficiency is not based solely on equipment quality. It results from the correct pairing of pump technology with operational needs, careful attention to design parameters, and ongoing monitoring of performance indicators.
Efficient vacuum performance depends on how well a pump achieves its required pressure while consuming the least possible energy and experiencing minimal wear. Performance varies depending on pump type, ambient conditions, and system layout. At Stanpumps, every vacuum solution is designed with measurable efficiency gains in mind—especially in sectors like packaging, food production, pharmaceuticals, and chemicals.
The energy used to generate a vacuum accounts for a large part of system operating costs. Optimising this begins with the right engineering, where Stanpumps helps align pump capability with production output and application scope.
Every vacuum pump type has a unique efficiency profile. Dry claw pumps, oil-sealed rotary vane models, and roots booster pumps each serve different purposes. Matching the pump to the process ensures less strain and more stable vacuum generation.
For instance:
Stanpumps provides tailored solutions to ensure vacuum pumps match the exact system duty cycle and output requirements.
An efficient vacuum system depends on low resistance, minimal leak points, and properly sized piping. Shorter distances and direct routes between the pump and application point reduce pressure drop. Incorrect pipe sizing and poor layout cause performance losses.
To support this, Stanpumps ensures correct integration of pumps into new or existing systems to avoid oversizing or unnecessary operational load.
Even minor leaks in a vacuum system can lead to significant inefficiencies. These leaks force the pump to work harder, increasing wear and energy use. Stanpumps provides technical support for leak testing and uses materials suited to the specific operating environment to ensure seal integrity.
In applications where contamination is a concern, particularly in food, pharma, or electronics, using the right sealing components and vacuum-compatible valves further enhances system integrity.
For oil-sealed pumps, degraded oil leads to loss in compression efficiency and potential contamination. Monitoring oil quality and changing it at recommended intervals maintains consistent vacuum levels and protects internal components.
Dust and vapour filters, when blocked or saturated, restrict airflow and reduce efficiency. Stanpumps advises scheduled filter changes based on usage cycles and environmental conditions to prevent unnecessary energy draw.
Vacuum pumps with electric motors should be monitored for load fluctuations. Changes in power consumption could indicate mechanical inefficiencies or system blockage.
By using variable frequency drives (VFDs), Stanpumps enables vacuum pumps to adjust output in real time based on demand. Instead of running at full speed continuously, the pump modulates its output—saving energy and extending component life.
Adding a buffer tank or reservoir to a system helps maintain stable pressure during fluctuations. This reduces pump cycling and improves system responsiveness in batch processes or packaging lines.
Real-time monitoring allows early detection of vacuum losses, motor strain, or filter blockages. Stanpumps offers solutions integrated with IoT systems for data logging and predictive maintenance.
Stanpumps not only supplies vacuum pumps but also designs end-to-end solutions based on pressure requirements, application constraints, and energy targets. Whether designing systems from scratch or upgrading existing installations, Stanpumps provides guidance that leads to higher reliability, longer equipment life, and reduced downtime.
In high-volume sectors like dairy processing, vacuum packing, or electronics manufacturing, the benefits of efficiency multiply. By helping companies reduce over-specification and improve flow design, Stanpumps ensures better return on investment and environmental responsibility.
Efficiency improvements start with choosing the correct equipment. Stanpumps offers a range of models for specific needs:
These pump types have been engineered to deliver precise vacuum levels without overloading systems. Their consistent performance, when paired with intelligent layout and controls, drives measurable gains in operational efficiency.
If you’re looking to reduce operational costs, increase output reliability, and optimise your vacuum processes, Stanpumps offers expert engineering support and robust vacuum technologies. Every solution is tailored to fit the demands of your operation, ensuring long-term value and consistent system performance.
Ready to optimise your vacuum process?
Contact the team at Stanpumps today to learn more about efficiency-focused vacuum pump systems and maintenance strategies.